The LED display cabinet calibration can greatly improve the display quality of the spliced display screen, and it is more efficient than on-site calibration, and is not limited by time and venue, and the cost is also low. Therefore, the cabinet calibration technology will become an indispensable part of the LED display manufacturing process and has a good application prospect.
Due to the discreteness and attenuation of LED light-emitting tubes and the discreteness of circuit components, LED display screens have inconsistent brightness and chromaticity, which seriously affects the display quality. In order to overcome the problem of LED display brightness and chromaticity non-uniformity, point-by-point correction technology came into being and developed rapidly. It can significantly improve the uniformity of the LED display and improve the display quality.
According to different applications, the point-by-point calibration technology can be divided into two types: one is the box-by-box calibration on the production line (box calibration); the other is the on-site large-screen calibration (on-site calibration). On-site calibration technology can select a suitable viewing location for calibration to ensure that the LED display achieves a satisfactory display effect in the on-site application environment.
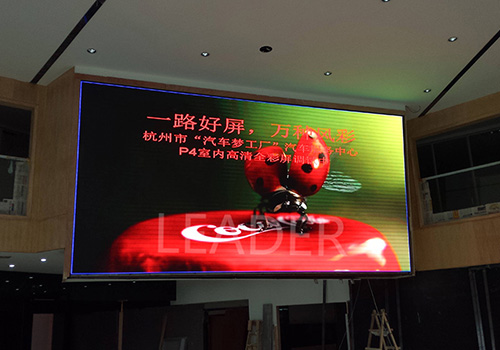
Cabinet calibration is a kind of production line calibration, and LED display manufacturers are required to add this link in the production line. Under normal circumstances, the cabinet calibration is the last link arranged before leaving the factory. It is mainly used to eliminate the difference in brightness and chromaticity between the inside of the cabinet and the cabinet, and to improve the uniformity of the LED display after splicing.
The cabinet calibration needs to be carried out in a dark room, and it needs to be equipped with an area array imaging device and a colorimeter to measure the brightness and chromaticity information of each cabinet. In order to ensure that the calibration process of all cabinets is not affected by external environmental conditions and achieve the goal of consistency of brightness and chromaticity, the dark room is required to be completely sealed, and the temperature and humidity are constant values. During the calibration process, it must be fixed. For the position of the cabinet and the calibration instrument, the cabinet must be placed on the base to avoid the influence of ground reflection.
Similar to on-site calibration, for each cabinet, the process of cabinet calibration includes data collection, data analysis, target value setting, correction coefficient calculation and coefficient upload. It also requires the cooperation of the control system.